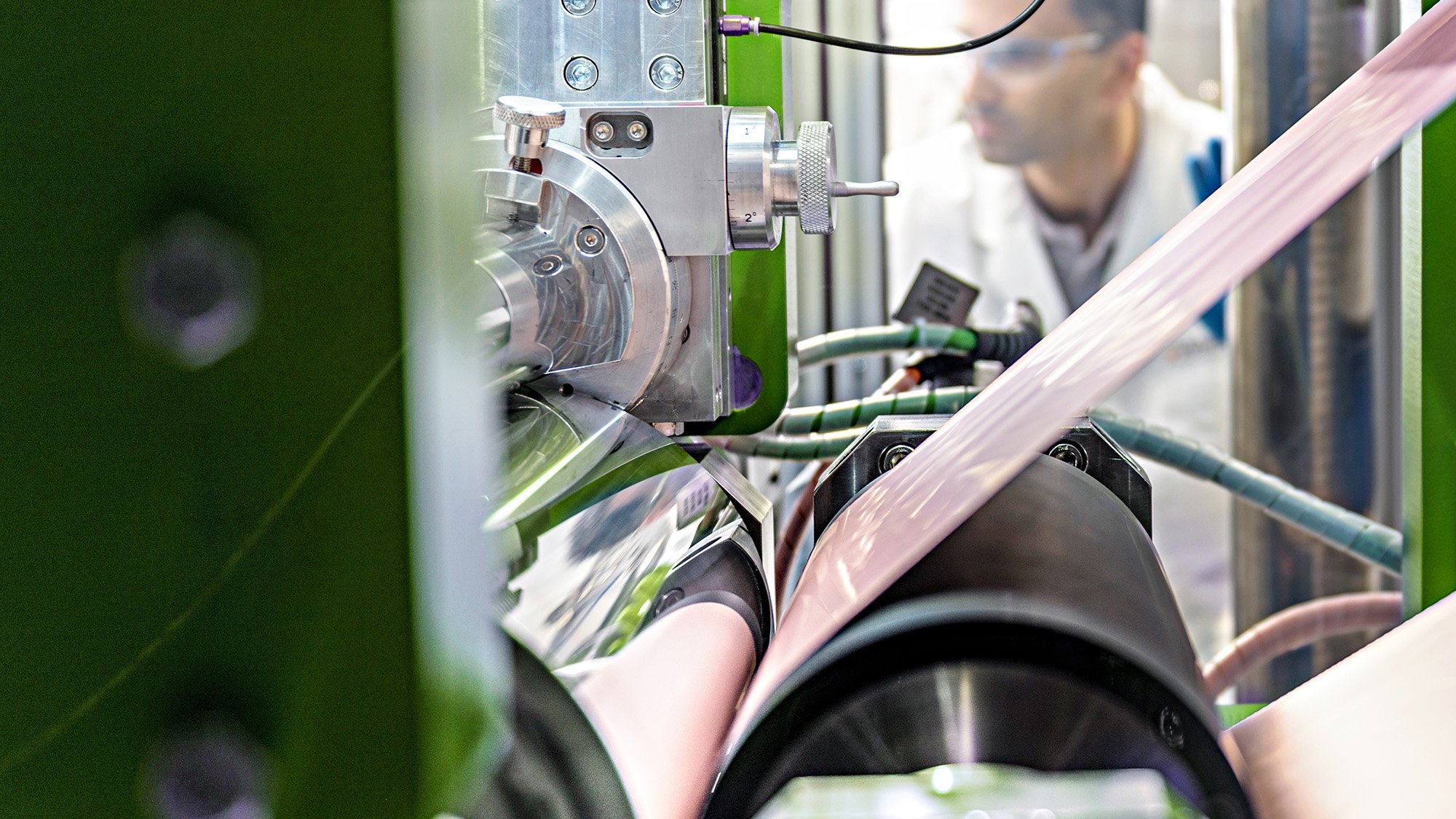
Produkcja akumulatorów
Czy to w samochodach elektrycznych, w systemach magazynowania energii odnawialnej, czy też w urządzeniach przenośnych – akumulatory zaspokajają obecnie nasze zapotrzebowanie na energię i są wyrazem zachodzącej transformacji energetycznej.WAGO angażuje się w tę zmianę i wspiera swoją ofertą producentów baterii, ogniw i akumulatorów. Oferujemy odpowiednie rozwiązania do pomieszczeń sterylnych, od sterowania temperaturą po zarządzanie danymi o zużyciu energii.