Protection Against Corrosion
18 September 2019The Galvanizer
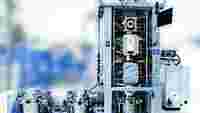
New methods developed by using hot-dip simulators: The WAGO I/O SYSTEM functions as the central communication system.
Zinc is a particular material that shifts the expiration date of iron far in the future. It safely protects steel from corrosion, so that galvanized components do not rust. This is because zinc and iron form an inseparable elemental compound – the common ferro-zinc alloy. However, this method employs poisonous and potentially explosive gas atmospheres at high temperatures. This consequently demands a process control system that is quite sophisticated to guarantee safety. The task of constantly refining these processes falls to Surtec Research and their hot-dip simulators. The engineers from Falk Steuerungssysteme use the space-saving, easily integrated WAGO 750 I/O SYSTEM in the automation systems for the simulators.
Hot-dip galvanizing is not a new process. The earliest industrial examples extend back into the mid-1800s. However, even after more than 150 years of refinements, improvements to the process still make sense. Due to the increased strength of the steel sheets used in automotive manufacturing, in particular, they are now considerably thinner. Yet the demands placed on the corrosion protection have only increased. “Modern automobile steels are only coated under certain circumstances, due to the variety and characteristics of their alloy components,” explains Björn Beißner, Project Manager at Falk. Safely coping with these challenges on an industrial scale means prior testing of new alloys, gas atmospheres, temperature curves and processes at a laboratory scale. Surtec Research, headquartered in Düsseldorf, builds annealing and hot-dip simulators for this purpose (www.surtec-research.com), and Falk Steuerungssysteme from Stadthagen in Lower Saxony develops and programs the entire automation system. The essential challenge consists in transforming the continuous passage process, found in galvanizing systems, into a dip process, so that the lab results can be transferred into production on a one-to-one basis.