Our MCS Product Finder
For the right wire-to-wire, wire-to-board, or board-to-wire pluggable connector for your application, try our new MCS Finder. It just takes a few steps and WAGO will find the right part for you.
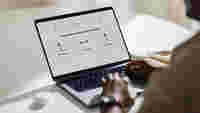
Our Literature Finder
Quickly find WAGO brochures and product catalogs with our new Literature Finder. Simply answer a couple of questions and download the materials you are searching for…it’s that easy!