The Right Automation for Modular Machines
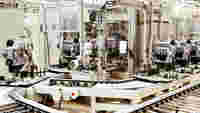
Automation in mechanical engineering:
- Custom Automation Architecture
- In the Control Cabinet or Directly on the Machine
- Modular Automation for Specialized Machines
For optimal implementation of a modular concept in specialty machine construction, the automation should be based on a modular design. The WAGO 750 Series I/O System and 767 Series SPEEDWAY offer specialty machine builders the perfect tools for this purpose. The variety of possible input and output signals and the possibility of combining standard inputs and safety-relevant inputs in one system offers system engineers tremendous flexibility.
By Jürgen Pfeifer | 2016-10-10
WAGO at Work
Customer Applications from the Area of Production Technology
As a partner and innovation leader, WAGO implements many interesting projects. Learn more about our creative and efficient production technology solutions.
CNC drilling machines from Schmoll are used worldwide. They employ WAGO TOPJOB® S Rail-Mount Terminal Blocks for wiring their electrical systems.
To monitor its production equipment, Schaeffler uses fieldbus couplers from WAGO, which make fault message processing significantly more elegant.
At Nordson, a wide variety of machines are produced in record time. WAGO’s automation technology and e!COCKPIT Engineering Software make this possible.
This May Also Interest You
Other WAGO Topics
Saving energy is good for the environment and for business. Performing the right analysis and taking the right steps can lead to sustainable profit. WAGO is your partner for effective energy management.