Precise Management of Testing Processes
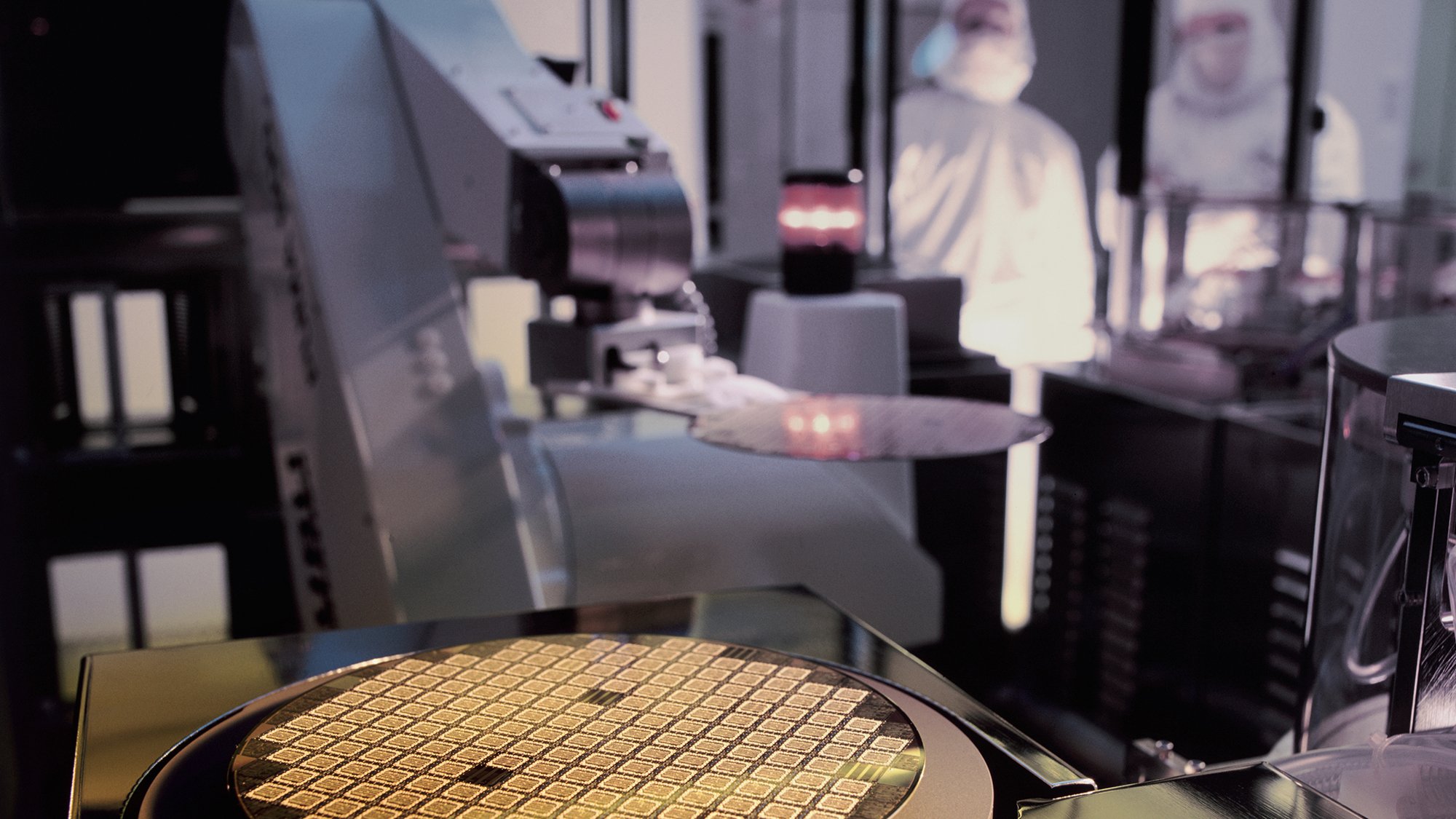
Operating rooms and pharmaceutical production facilities have one thing in common: They require cleanroom technology to ensure patient safety and the quality of production environments. Topas is a technology leader in this field. When testing filter media, such as those required for air filters in cleanrooms, Topas relies on control technology from WAGO.
Cleanroom technology is the key technology in many applications. For example, it is used for medical treatments in operating rooms, in the pharmaceutical industry and in production facilities for microelectronics, where it keeps the quantity of airborne particles introduced into or created within the room as low as possible. This is essential in order in order to treat patients safely and protect products from harmful particles.