Fashion Forward with WINSTA®
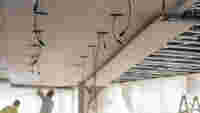
Zinser, a fashion house in Tübingen with a rich tradition, is undergoing modernization and will soon be brilliantly illuminated by 7,500 LEDs. In order to install the lights in the shortest possible time – and during ongoing sales operations, no less – Elektro Kürner GmbH relies on the WINSTA® Pluggable Connection System from WAGO.
This kills several birds with one stone. First, the installation can be completed in the very short time period required. Second, mismating during installation of the lights is virtually impossible. Third, maintenance of the lights will be much easier in the future.