Condition-Based Monitoring of Rolling Stock
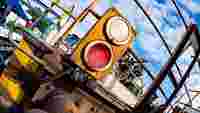
“Condition-based monitoring” promises to make maintenance of railway vehicles more efficient, in terms of both time and costs. Westfälische Lokomotiv-Fabrik Reuschling GmbH & Co. KG shows how railway operators can implement condition monitoring for their rolling stock.
The way locomotives are driven determines how quickly components wear or operating materials age. Therefore, it makes sense to monitor railway vehicles on a continuous basis. This process is called “condition-based monitoring.” “If we know what the loads are, we can maintain the vehicles dynamically. But to do that, we need data” explains Udo Pinders, Managing Director of Reuschling. Westfälische Lokomotiv-Fabrik is well known throughout Europe as a reliable expert partner for maintenance and modernization of all types of railway vehicles.
For effective service and condition-based maintenance, this company, from Hattingen in North Rhine-Westphalia, relies on a modular system with a cloud connection. In the process, automation technology from WAGO forms the interface to a Web-based system for fleet management of rolling stock – the J.I.M. Portal, which stands for “job-based intelligent monitoring.” What that means is: Instead of only paying attention to hours of operation, condition-based monitoring makes it possible to replace wear parts and operating materials only when really necessary.
Condition-Based Monitoring – Here’s How Wago Supports You:
A modular system with cloud connection: WAGO forms the powerful interface to the Web-based J.I.M. portal.
200 measured values per second: Since processing with CODESYS was no longer possible, the XTR Controller programming was done on the basis of Linux®.
Pressure, temperature, acceleration: Condition-based monitoring makes it possible to draw conclusions about the driving behavior of a locomotive driver, for example.