Safety Technology from the Process Industry Prevents the Spread of the Virus
Process Technology for Fighting the Pandemic
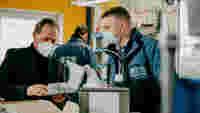
Those who work in early risk detection are welcome guests in chemical facilities and their control rooms. When discoveries used to monitor reactors and surplus gas burners can then be transferred to the protection of thousands of people during a pandemic, then the invitations to set up pilot applications pile up quickly. This is exemplarily demonstrated by an automated body temperature check at the turnstiles used to contain the Corona pandemic.
Reasons for WAGO:
Early risk detection using industrial thermal cameras
Automated body temperature check using Prometheus
System only functions by combining industrial camera technology with intelligent controllers
Direct communication with the cameral electronics thanks to WAGO Digital Plant Gateway