Automating Sawing Equipment
with the I/O system in IP67
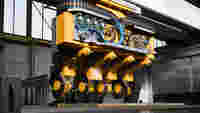
Burkhardt-Löffler, located in Franconia, manufactures systems for stone working, and relies on consistent automation from WAGO. The WAGO I/O System Field ensures the necessary connectivity in their newly developed saw. The solution scores points with its easy cabling, free parameterization of the inputs and outputs, IP67 protection class, and fast implementation, among others.
Limestone from Jura in Franconia has long been valued: from the Romans to the builders of Medieval churches and palaces, up to the present. Its warm hue provides buildings with a particularly prized appearance. The region that lies between Nuremberg and Ingolstadt has brought forth more than just a globally desirable building material. It is also the birthplace of an international leader in the manufacture of systems for processing this and other types of stone: Löffler from Langenaltheim near Eichstätt, merged in 2017 with Burkhardt-Hensel from Bayreuth to form Burkhardt-Löffler.
With its large base of customers, primarily in central Europe, North America and Australia, Burkhardt-Löffler is currently represented in several countries around the world. Customers use the systems to produce, for example, kitchen counters from natural and artificial stone and ceramics. These projects require high precision as cutouts for sinks or cooking surfaces must be milled to within fractions of millimeters. Manufacturing panels for building facades, another application field for these systems, also demands great care.
The IP67 I/O System Field offers high connectivity for the field level.
Customers profit from the high degree of flexibility incorporated into the system with its individually and variably parameterizable inputs and outputs.
Installation and implementation of the solution are easily carried out.