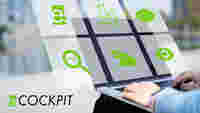
Programming and Configuring with e!COCKPIT
WAGO’se!COCKPIT Automation Software expedites machine and system startup, while reducing development times for automation projects! Ensuring a project’s long-term viability through sustainable cost savings hinges on a user’s ability to quickly adapt to new software that offers a high degree of reusability. e!COCKPIT is an integrated development environment that supports every automation task from hardware configuration, programming, simulation and visualization up to commissioning – all-in-one software package.
Your Benefits:
- Integrated engineering
- A smart design
- CODESYS 3
- Graphical network configuration