Explosion Protection for Humans and Machines
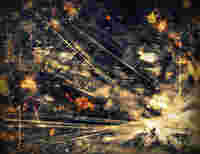
The topic of explosion protection originated in mining. Mixtures of methane and air that arise in coal mining and are explosive in a certain ratio were handled with controlled explosions until the second half of the century. But how does it work now?
Flaring off firedamp is no longer necessary due to a number of technical achievements and protection regulations. However, the topic of explosion protection has not lost its importance despite all this. It is now widespread not only in mining, but also in other industries, because explosive materials are also present there. Common examples include the chemical industry, during the production of crude oil or natural gas and in the food industry.
Your Benefits at a Glance:
- Economical system operation
- Short start-up and service times thanks to modular concepts
- Reduced operating costs thanks to maintenance-free and vibration-proof connection technology
- Adjustments can be made quickly thanks to optimum form factor and versatility