Safely Fill Explosive Substances in EX Areas
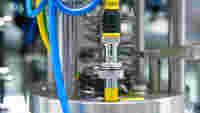
They may be green, gray, red, blue or black, but they always contain 200 liters. Internationally standardized steel drums are widely used to fill potentially hazardous liquids, such as oils and chemicals, into robust packaging. To fill these drums, Feige FILLING has developed a turnkey filling line that also includes both handling and material flow processes. “Our customers want to fill and ship their products. They do not want to worry about how the drums arrive under the fill valve or will later materialize on the shipping pallet,” says Marketing Manager Martina Thomsen. She adds that drums are just one of many packaging types that the Feige FILLING systems can accommodate. “The spectrum ranges from 1 m³ IBCs and drums to small containers, such as paint buckets from the hardware store.”