Bezpieczna kontrola procesu cynkowania
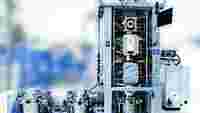
Cynk jest substancją, która zapewnia długi czas użytkowania, chroni stal przed korozją. Elementy cynkowane nie rdzewieją. A pierwiastki cynku i żelaza tworzą nierozdzielny związek – stop żelazo-cynk. Podczas tworzenia stopu występują wysokie temperatury w atmosferze gazów toksycznych i potencjalnie wybuchowych. Dlatego tak istotna jest bezpieczna kontrola tego procesu. Jego realizację trzeba wciąż udoskonalać, a to jest zadaniem symulatorów zanurzeniowych Surtec Research. Firma Falk Steuersysteme GmbH stosuje w nich kompaktowy, wysoce zintegrowany WAGO I/O System 750.
Cynkowanie ogniowe nie jest niczym nowym. Pierwsze procedury cynkowania w skali przemysłowej sięgają połowy XIX wieku. Ponad 150 lat później wciąż warto ulepszać tę sprawdzoną metodę. W przemyśle motoryzacyjnym stosuje się dziś blachę stalową, która dzięki większej wytrzymałości może być coraz cieńsza. Równocześnie rosną wymagania w zakresie ochrony antykorozyjnej. Nowoczesne stale samochodowe, ze względu na dużą różnorodność i właściwości składników stopów, należy cynkować tylko w bardzo określonych warunkach", wyjaśnia Björn Beißner, kierownik projektu w firmie Falk. Jest to problem, którego rozwiązanie na dużą skalę oznacza przetestowanie w warunkach laboratoryjnych nowych stopów, atmosfer gazowych, krzywych temperaturowych i całych procesów. Firma Surtec Research z siedzibą w Düsseldorfie buduje symulatory wyżarzania i topienia (www.surtec-research.com), dla których firma Falk Steuersysteme GmbH z Stadthagen w Dolnej Saksonii zaprojektowała i zaprogramowała cały system automatyki. Głównym wyzwaniem jest przeniesienie procesu cynkowania do procesu zanurzeniowego w taki sposób, aby wyniki laboratoryjne można było później jeden do jeden przenieść do produkcji.