Heeling Compensation
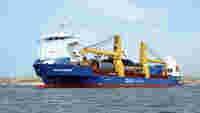
The stability of mobile cranes on land is comparatively easy to ensure; a suitable counterweight is set based on the load, and a few minutes later, hydraulic supports extend several meters outwards for balance. However, it is commonplace for bulky and especially heavy loads to be transported to their destinations primarily via water. This raises the question as to how stability is ensured for onboard cranes – water is known as an unstable surface. Systems made of pumps, valves and ballast tanks hold cargo and commercial ships upright. Often called “heeling pumps,” these systems prevent listing of the ship’s body in the case of unevenly distributed loads. To control them, the specialists at BESI rely on WAGO's PFC200 Controllers in combination with the WAGO-I/O-SYSTEM 750 for Ex and non-Ex areas.
Vessels which can be identified from afar are called “MPV Heavy Lifters,” as they have at least two large cranes on deck. These multi-purpose vessels are designed specifically for handling bulky and heavy cargo. According the Michael Borchers, Chief Technical Officer at BESI, their cargo has included rocket parts, turbines and even entire trains. In a current new construction project, the two cranes of one “MPV Heavy Lifter” can exceed 1500 metric tons of lifting capacity. The heeling compensation systems on such ships have to be designed with corresponding abilities.
Tank Ballast and Cargo Management – Here’s How WAGO Supports You:
- Automation and communication technology from WAGO has all of the necessary approvals for maritime use, so it meets international standards.
The modularity of the WAGO-I/O-SYSTEM guarantees flexibility and allows custom adaptation and expansion of the automation.
The WAGO-I/O-System offers a high degree of functionality in a compact design.