Monitoring Dangerous Goods Reliably with Maritime Products from WAGO
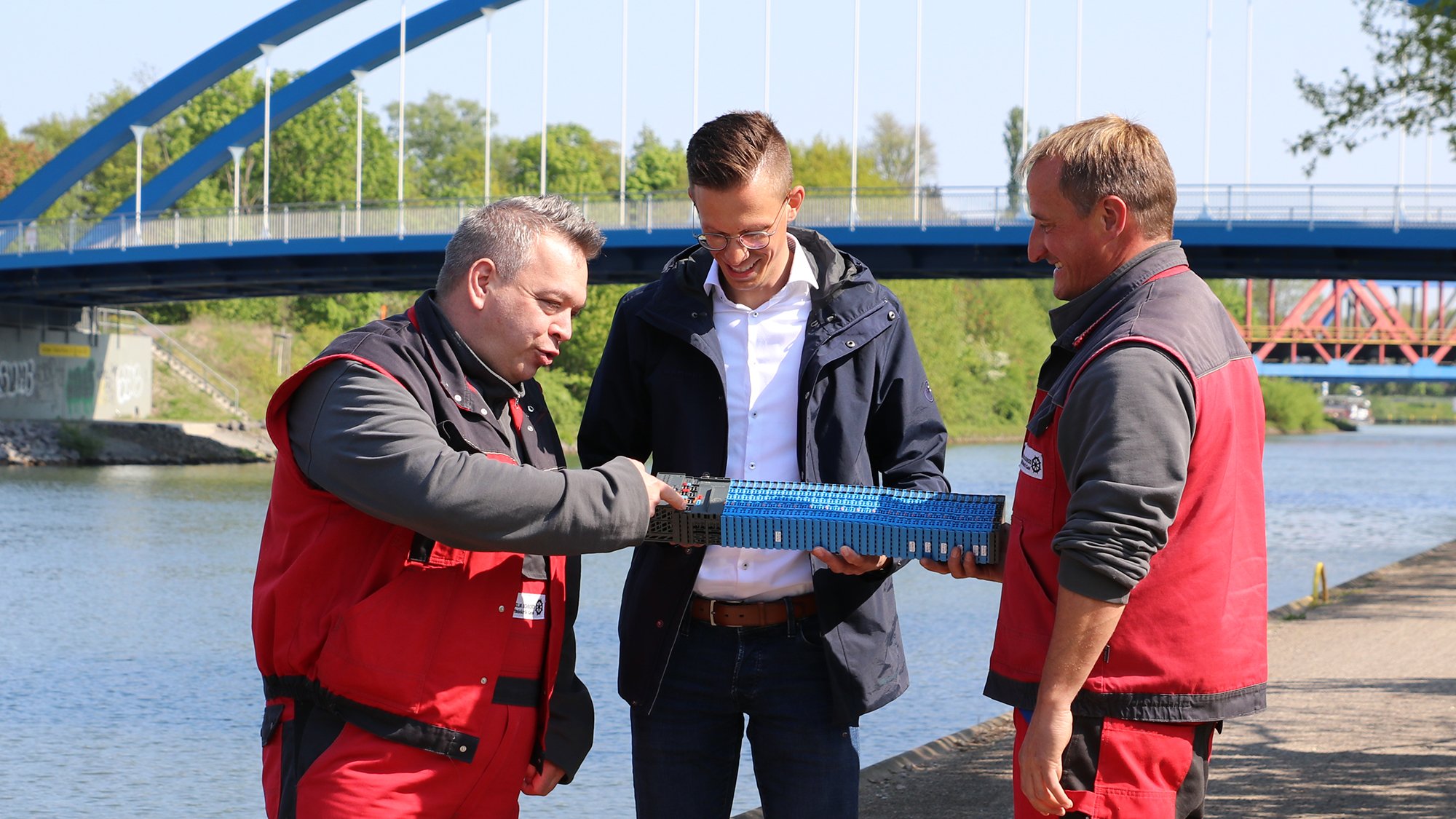
Since 1963, Wilhelm Schroer Schiffselektrik GmbH, headquartered in Duisburg, has provided services, class renewals and upgraded electrical systems for inland shipping throughout Europe. “Our core businesses include maritime electronics, customer service, repairs and upgrades,” says Master Electrician Christian Möhlenbruch, describing the company’s main focus areas. Since the requirements on inland vessels are very complex, and the legal and regulatory details change almost every year, this family-owned company’s technicians are always busy designing and implementing systems to comply with them. Above all, this involves digitization and automation of ship operations, which are becoming more and more digital all the time. One of the recent projects relates to tank warning systems for ships that transport dangerous goods in liquid or gas form. The tanks on these ships must be monitored constantly with a specialized warning system. Since every ship is different, no two tank warning systems are the same. Therefore, Christian Möhlenbruch and his colleagues develop tank warning systems that are tailored to the specific vessel. However, these systems do have one thing in common: They all include maritime products from WAGO.