2010-2019
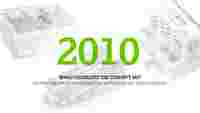
The Founding of WAGO
11 March 2024WAGO Shapes the Future
The world turned its attention to the challenges and opportunities created by digitalization, and WAGO was at the epicenter. Whether cybersecurity, cloud connectivity or software applications, WAGO continued developing automation solutions focused on openness and flexibility. In addition, WAGO introduced DIMA (Decentralized Intelligence for Modular Applications) in 2014, a method that blazed new trails in process automation. However, the products were also being further developed that catered to the user’s interest in electrical connection technology: Since 2014, the 221 Series Installation Terminal Block has fascinated customers, and the new WAGO TOPJOB® S Rail-Mount Terminal Blocks with levers will be even easier to use in the future.
Product Developments and Events from the 2010s
2012
WAGO’s Automation Solutions Shape the Future
The all-in-one solution for the challenges of digitalization does not exist, but there are smart products, methods and partners. WAGO offers its customers concrete solutions based on technologies that offer measurable added value to users. Whether building automation, cloud connectivity, cybersecurity or digital engineering. WAGO’s automation solutions and products rely on simplicity, openness and innovation, and they support digitalization in customers’ companies. For example, since 2012, with flexROOM®, WAGO has offered a variable concept for building automation that combines hardware and software to individually regulate sun protection, temperature and light. The motto is clear: Easy configuration instead of complex programming. WAGO’s controllers are also evolving. Since 2013, the fieldbus-independent controllers from the PFC family have been WAGO’s answer for control tasks in buildings and industry. Today, a simple software update turns them into an IoT controller with cloud connectivity. Data from the field level can now be easily aggregated and analyzed, making companies and systems future-proof.
2012
Industry 4.0 – Digitalization at WAGO
The world is discussing the definition, challenges and opportunities of Industry 4.0, and WAGO has also been successfully pursuing the path of digitalization for many years. The General Secret of Digitalization at WAGO: Simplicity and Openness. The goal: speed, efficiency and flexibility. This also applies to WAGO’s production processes. The global networking of systems in WAGO’s production facilities yields data in near real-time, from which KPIs are generated and visualized. By using KPIs, production processes can be continuously analyzed to generate constant improvements. The result: fast, reliable, economical production.
Solution Openness with WAGO
The advancement of digitalization means swiftly increasing levels of complexity, primarily in automation processes. Manufacturers must be capable of responding in increasingly shorter time spans. This becomes particularly noticeable within the chemical, industry, food, cosmetics and pharmaceutical sectors. However, it is both too expensive and too slow to convert classic processing systems. WAGO recognized the trend and asked: How can we support our customers? What opportunities does digitalization offer here? In 2014, WAGO sponsored the general meeting of NAMUR, an acronym derived from the German Association for Standardization of Measurement and Control Engineering in the Chemical Industry, now called the User Association of Automation Technology in Process Industries. The topic was decentralized intelligence. An opportunity to put a once-vague idea into practice and present it to an expert audience. The result: DIMA (Decentralized Intelligence for Modular Systems). A revolutionary method for automating process systems.
DIMA – The Process Automation Revolution
In November 2013, WAGO began a research project with the Technical University of Dresden and the Helmut-Schmidt University of Hamburg. With a lot of trust, perseverance and comprehensive expertise, WAGO accomplished in months what had previously taken years. The first prototype of DIMA (Decentralized Intelligence for Modular Systems) will be presented as early as November 2014. Instead of working with rigid system structures, DIMA functions with an open system architecture. Digital descriptions of process modules and open, manufacturer-independent communications form the foundation. They enable cost-effective engineering in addition to the flexible incorporation, expansion, and conversion of intelligent modules. Additional advantages: Shorter design phase, fast system design, rapid commissioning and maximum flexibility by adapting module capacities to market conditions. Thus, the end game of digitalization is not a lock-out but freedom of choice. Customers are impressed and are actively integrated into further developments by DIMA. This pays off: To date, DIMA has already received four innovation prizes and has become NAMUR’s recommendation – a real accolade for WAGO’s solution.
2018
WAGO’s electrical interconnection products deliver what they promise: easily, safely and quickly. However, if others think a product has peaked, WAGO will gladly revisit it. WAGO proved this in 2014 by further developing the 222 Series Splicing Connector. WAGO's new 221 Series Splicing Connector simplified operation. Just four years later, the lever technology of the 221 Series joined the rail. The result was the TOPJOB® S Rail-Mount Terminal Blocks with Lever, which WAGO introduced at the Hanover Fair in 2018. With this technology, wires can be terminated and removed by hand, without tools – even in the control cabinet: Lift the lever, insert a conductor, close the lever. In addition to the ease of handling, the user now has both hands free for wiring. WAGO naturally maintained the original advantages of TOPJOB® S rail-mount terminal blocks, demonstrating yet again that WAGO always emphasizes customer use when refining its own products.
2018
The WAGO 221 Success Story
The 222 Series Splicing Connector: excellent functionality and enthusiastic customers. And yet. At WAGO, you're certain that more is possible. Therefore, in 2014, WAGO reinterpreted the proven 222 Series Splicing Connector with the new 221 Series Splicing Connector. The focus was on improved, simplified handling for the user. The result: 40% less volume for space-saving installation, a transparent housing for easy contact testing and even easier handling: Pull the lever up, insert a conductor and push the lever back down. The customer response was more than enthusiastic. Whether for the 1,700 meter LED ribbon in the cinema hall, the wastewater pump system at 2,000 m, a light matrix at the Open Air Festival or for networking in sustainable vegetable cultivation – the 221 Series Splicing Connector inspires customers in a wide variety of industries and turns them into connection heroes.
Get insight into other decades of WAGO corporate history here